Tangential Flow Filtration (TFF) is a sophisticated filtration method used extensively in the biopharmaceutical industry for the concentration, desalting, and purification of biomolecules. Unlike conventional filtration techniques where the feed flows perpendicularly through the filter, TFF processes fluid tangentially across the surface of the membrane. This approach minimizes the accumulation of retained species on the filter surface, reducing fouling and improving efficiency. This comprehensive guide delves into the mechanisms, applications, advancements, and critical considerations in TFF technology.
Understanding Tangential Flow Filtration
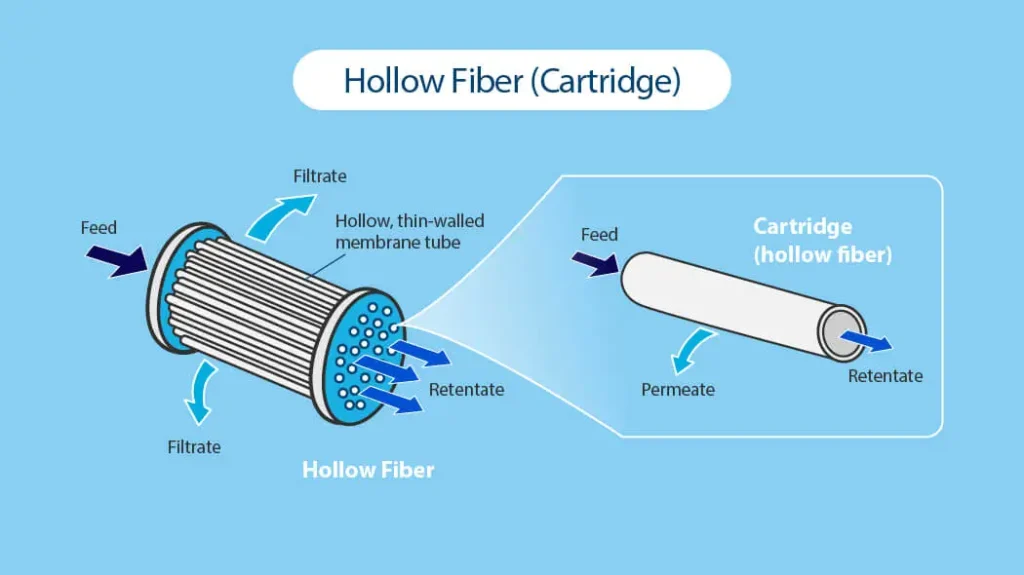
1. Basic Principles Tangential Flow Filtration operates on the principle of crossflow filtration. The liquid stream (feed) flows tangentially along the membrane surface, while the pressure drives a portion of the fluid through the membrane, separating it into filtrate (permeate) and retentate (concentrate). The crossflow of the feed across the membrane prevents the build-up of particles and solutes on the surface, thereby maintaining a high flow rate and efficient separation.
2. Membrane Types and Selection Membranes used in TFF are typically made from polymeric materials such as polysulfone, polyethersulfone, or regenerated cellulose. The choice of membrane is crucial and depends on factors like:
- Chemical compatibility with the feed.
- Pore size, which ranges from ultrafiltration (UF) to microfiltration (MF) scales.
- Mechanical strength and operational stability.
3. Process Parameters Key parameters influencing TFF efficiency include transmembrane pressure (TMP), crossflow velocity, feed concentration, and temperature. Optimizing these parameters is essential for maximizing yield and purity while minimizing processing time and cost.
Applications of Tangential Flow Filtration
1. Biopharmaceutical Manufacturing In the production of therapeutic proteins and vaccines, TFF is used for the concentration and buffer exchange of bulk drug substances. It ensures the removal of impurities and adjusts the formulation to the required final concentration.
2. Water Purification and Wastewater Treatment TFF systems are employed in the removal of contaminants from water and the concentration of valuable components from wastewater. They are particularly effective in applications requiring the retention of large molecules or particles.
3. Dairy Industry In dairy applications, TFF is used to concentrate proteins in milk and whey, enabling efficient processing and formulation of dairy products like cheese and yogurt.
4. Food and Beverage The concentration and clarification of juices, extracts, and other food products are facilitated by TFF, improving product stability and shelf-life.
Technological Innovations in TFF
1. Module Design Innovations Recent advancements in module design, such as the development of spiral-wound and hollow-fiber modules, have significantly increased the surface area available for filtration, enhancing the efficiency and capacity of TFF systems.
2. Automation and Process Integration The integration of TFF systems with automated process controls has improved the reproducibility and scalability of filtration processes. Real-time monitoring and control of flow rates, pressure, and concentration have streamlined operations and reduced the need for manual intervention.
3. Sustainable Practices Innovations aimed at reducing the environmental impact of TFF processes include the reuse and recycling of membranes and the reduction of water and energy consumption. These practices not only lower costs but also align with global sustainability goals.
Challenges and Future Directions
1. Fouling and Membrane Life Despite the advantages of TFF in minimizing fouling, membrane lifespan remains a challenge. Research is ongoing into more resistant membrane materials and cleaning protocols to extend membrane life.
2. Scale-up Challenges Scaling TFF processes from laboratory to industrial scale involves complexities related to flow dynamics and system design. Customized solutions and pilot testing are critical for successful scale-up.
3. Regulatory Compliance In pharmaceutical applications, TFF systems must comply with stringent regulatory standards for cleanliness, traceability, and validation. Staying updated with regulatory changes and ensuring compliance is crucial for manufacturers.
Conclusion
Tangential Flow Filtration represents a critical component in modern manufacturing and environmental management, offering precise, efficient, and scalable solutions for a variety of separation needs. As technology advances, the future of TFF looks promising with potential enhancements in membrane materials, system design, and automation poised to further revolutionize this field. By continuously improving and adapting TFF technologies, industries can achieve higher efficiency, better product quality, and increased sustainability.